The Business Leaders' Forum Newsletter
The ‘lean’ path to ESG success
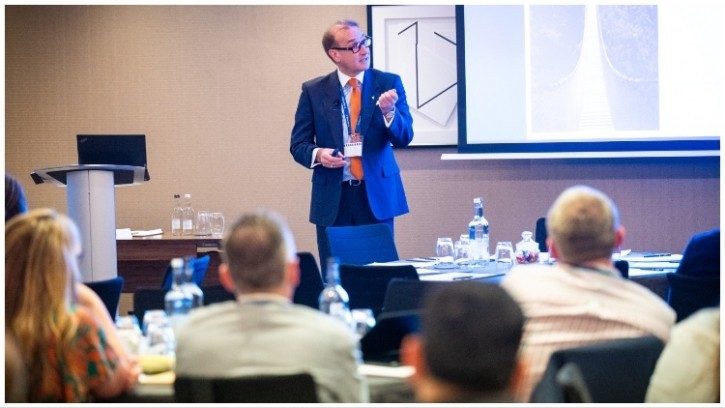
Lean manufacturing is a philosophy that comes with an impressive history.
Although there are examples of process thinking from as far back as the 1450s and the Arsenal in Venice (a complex of former shipyards and armories in the city of Venice), the example probably most frequently given is the production model of Henry Ford in the early years of the 20th century.
Whilst the Ford manufacturing system removed inefficiencies and achieved never-before attained levels of manufacturing quality and consistency, it had a significant flaw. This was best summed up by Henry Ford himself, when he allegedly offered car buyers ‘any color the customer wants, as long as it’s black’.
As consumer expectations moved increasingly towards choice, the Ford model struggled until, in the 1930s, when other industrialists turned their thoughts to this new challenge. Kiichiro Toyoda, Taiichi Ohno and others at Toyota began to introduce a series of innovations into their production processes that enabled Toyota to provide both continuity in process flow as well as variety in production offerings. The scene was set for the growth of 'lean manufacturing’.
In the Toyota Production System, the focus was shifted away from individual machines, towards the flow of a product through the entire process. Toyota concluded that by right-sizing machines for required volumes, introducing machine self-monitoring, lining machines up in a process sequence, pioneering fast setups so each machine could make small volumes of many parts, and ensuring each process step notified the previous step of its need for materials, it would be possible to obtain low cost, and high variety, quality and efficiency, alongside low-waste and rapid throughput production. Adoption of these principles in many companies globally, including food manufacturing, is testament to that conclusion.
At the heart of the lean philosophy is an emphasis on waste reduction and continuous improvement. In the context of ESG (environmental, social and governance) that makes lean a concept that was way ahead of its time.
Why are ESG and lean manufacturing good partners?
Lean is a methodology that focuses on minimising waste within manufacturing systems while simultaneously maximising profitability. It is therefore unsurprising that the first element lends itself well to achieving certain ESG goals.
Minimising waste throughout a manufacturing system means less environmental damage, more efficient working, less pressure on staff, potential savings for customers and consumers, and less demands made on the supply chain.
Whilst the lean methodology will not drive all your ESG commitments, it is certainly an important part of any manufacturer’s sustainability programme – both in terms of building a better, more profitable and more commercially sustainable business, and as a fundamental element of any integrated ESG plan.
How the ‘lean’ principles can help food producers
It is perhaps not surprising that lean manufacturing principles can play a crucial part in helping food manufacturers to achieve their ESG goals and aspirations.
By incorporating ESG considerations into the whole of the production and distribution process, food manufacturers can minimise their environmental impact, improve their reputation and reduce costs.
For any food manufacturer to succeed in all these ESG dimensions, the business must fully embed their ESG framework within their business model. ESG should not be seen as a ‘bolt on’ or a secondary requirement that is not integral to the business; it’s a way to ensure there is a positive impact on staff, customers, consumers and stakeholders, delivering against solid, ethical business principles and ensuring the business is ‘sustainable’ in every sense of the word. Value creation can be achieved in this way.
Embedding ESG into a lean food manufacturing system, removes any accusations that it might be a hinderance, given the emphasis of lean manufacturing on:
- Defining value
- Value stream mapping
- Creating flow
- Establishing ‘pull’
- Continuous improvement
By analysing a value-stream, or an entire end-to-end process, organisations can escalate the value of their ESG activities, benefiting the company enormously as well as the planet and its people.
Value stream mapping enables the food manufacturer to create the type of integrated system that is efficient, effective, consistent, and – that word again – sustainable.
As climate change and social pressures increasingly add to the risks, complexities and uncertainties faced by businesses, it has never been more important to develop a holistic business model. It is certain that climate-related legislation will continue to expand, capturing greater numbers of businesses as it does so. In addition, there will be more emphasis on global ‘levelling up’ as countries seek to benefit from the ESG efforts their organisations’ are making versus those in other locations with lower achievement thresholds. A good example of this is EU CBAM and from January 2027, UK CBAM. CBAM (the Carbon Border Adjustment Mechanism) seeks to apply a financial levy to companies importing certain goods from third-party companies with carbon emissions standards lower than those of the EU, and now the UK.
In addition, food manufactures are facing the triple challenges of hugely increased input costs, pressure on raw materials sourcing, and delivery and supply chain restrictions.
The more a company’s ESG commitments are integrated into its lean manufacturing model, the better able it will be to deal with all these complexities to the positive benefit of the business, its people, its customers and consumers, its supply chain, and the planet.
In a food manufacturing context, a reduction in defects and wastage, excess use of raw material inputs, preventable defects, costs associated with reprocessing defective items, and unnecessary product characteristics not required by customers is the very essence of efficient production, and as a result, greater environmental benefit.
Not all manufacturing companies operate on lean principles, but many food manufacturers do so; for most it is a small step from lean to ESG-lean.
Shortening changeover times, reducing over-production, improving inventory management, decreasing defects, standardising work processes, shortening lead times, lowering production costs, developing workforce flexibility, continuously improving operations and enhancing food safety are at the very heart of the lean manufacturing process for food manufacturers, but they are also at the heart of food-business sustainability in all senses.
The so-called ‘Four Ps’ of lean manufacturing embrace the very principles that ESG embeds, namely ‘purpose, process, people and performance’, which makes it an essential ally in fighting climate change and injustice in the world.
Essentially, process optimisation, not just in the production sense, but for every aspect of a food manufacturing business, is no longer just good sense, it really is now best practice.