Legal Brief
Cost pressures mount for F&B manufacturers following HSE fee hike
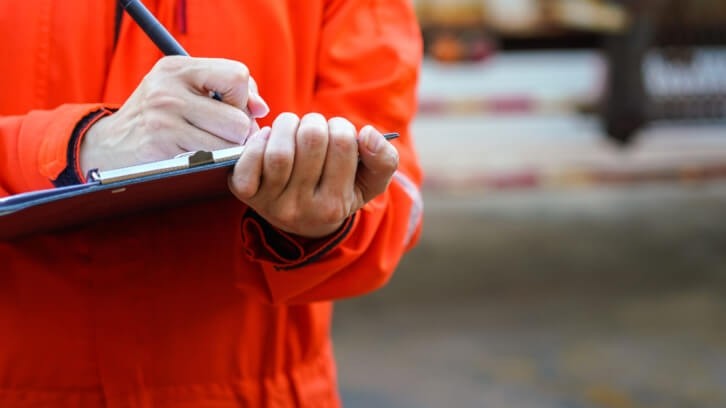
Food and beverage producers are now contending with increased health and safety compliance costs due to a recent rise in the Health and Safety Executive’s (HSE) ‘fee for intervention’ (FFI) charges. Having come into force 1 April 2024, these changes add to the already substantial cost pressures faced by the industry.
Since its inception in 2012, FFI has been a contentious aspect of HSE investigations. Unlike other investigative authorities, the HSE can charge businesses for the time spent investigating any material breach of health and safety laws. Recently, the hourly rate for FFI has increased from £166 to £174, a change intended to ensure the HSE continues to recover the full costs of regulatory activities.
This rate hike arrives at a challenging time for the food and beverage industry, which is already navigating complex operational challenges and must now prepare for potential added financial burdens.
What this means for F&B manufacturers
The food and beverage sector encompasses more than 30 distinct industries - including meat, poultry, grain mills, bakeries, fruit and vegetable processing, and beverage manufacturing – and faces unique health and safety challenges. Given the diversity across the different sub-sectors, compliance is certainly a multifaceted and critical concern.
Food safety is paramount, and any breach can have severe consequences, not just financially but also in terms of public health and brand reputation. The subjective nature of what constitutes a ‘material breach’ under HSE guidelines further complicates matters, leaving much to the discretion of individual inspectors.
Mitigating the risks of FFI
To avoid the financial impact of FFI, food and beverage producers must ensure their health and safety protocols are robust and meticulously followed. Embedding a health and safety mindset into the company culture is a crucial step. This involves regular training sessions, induction programs and continuous education about safety standards. This must be distilled from the ‘top-down’ i.e. the Board and senior management. Employees at all levels must understand the importance of adhering to safety regulations and be equipped with the knowledge to do so.
Developing and maintaining comprehensive health and safety policies is another critical measure. These policies should be well-documented and easily accessible to all employees. Regular internal audits and inspections are vital. These proactive measures can help identify potential hazards before they become significant issues, demonstrating a commitment to safety and compliance.
Having a clear, well-communicated incident response plan is equally important. It should outline immediate response actions, strategies to communicate with employees and the public, and protocols for liaising with authorities. The plan should cover more than just how to react directly to the incident on the ground, but also how it will be communicated to employees, who will manage media enquiries or liaise with relevant authorities and which external advisors need to be brought in. A thorough incident response plan not only helps mitigate the impact of an incident but also improves the HSE’s perception of a business during an inspection. It sends a clear message that the business is proactive in mitigating and managing risk.
Challenging an FFI
Despite best efforts, there may be occasions where an FFI is levied. Everyone has the right to challenge an FFI, and one positive change in recent years is that appeals are reviewed by an independent panel, not the HSE itself. However, disputing FFI can be costly and resource-intensive, with varying success rates. Therefore, obtaining an objective assessment of the likelihood of success before proceeding with a dispute can be invaluable.
In challenging an FFI, food and beverage manufacturers should keep comprehensive records of all health and safety measures, training sessions, audits and inspections. This documentation can be invaluable in demonstrating compliance and therefore whether any alleged breach is ‘material’. Consulting with specialist health and safety lawyers is recommended to ensure that all practices meet current regulations and standards and provide guidance on the appeal process if an FFI is issued.
Leveraging modern technology to monitor and enhance safety practices can also be beneficial. Automation and real-time monitoring can help identify risks early and ensure swift corrective actions. By prioritising safety, maintaining rigorous standards and being prepared to challenge FFIs when necessary, F&B producers can navigate these changes more effectively. Investing in preventative measures will not only mitigate the risk of incurring additional costs, but also create a safer and more compliant working environment.
FFIs are most certainly a case where prevention is better than cure. Food and beverage manufacturers are best served investing in the procedures and training that will mean they never have to worry about FFI – especially as the price of getting it wrong has just increased.
In other news, a new report has revealed the cost EUDR could impose on EU consumers.